По желанию клиента компания ПРОкабель может спроектировать, рассчитать, поставить а также выполнить работы по монтажу кабельных эстакад.
Скачать каталог по кабельным эстакадам (6,09 МБ) 
Скачать опросный лист для подбора эстакады (308 КБ) 
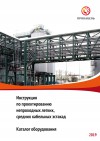

Во времена развитого социализма в нашей стране кабельные эстакады проектировались, исходя из требований ПУЭ, рекомендаций по привязке к конструкциям «ГлавЭлектроМонтаж» и наличием типовых чертежей на различные их виды. Все это было оправдано, т.к. основные советские стройки были большими и быстрыми в масштабах плановой, пятилетней советской экономики. Вспомним даже строительство завода КАМАЗ в Набережных челнах, который был начат в декабре 1969 года и уже в 1976 году сошел первый автомобиль, при этом комплекс заводов КАМАЗа раскинулся на 22 квадратные мили. В 90-е все изменилось, т.к. рыночная экономика требовала от предприятий быть более компактными, с высокой автоматизацией и эффективностью производства, мобильностью по изменению производственных площадок, то есть конкурентоспособными. К концу же 2010 года большинство предприятий России уже встали на рельсы эффективных закупок через торговые площадки и такие изменения потребовали от генеральных подрядчиков и электромонтажных компаний быть более мобильными при формировании цены на свои услуги, т.е. при том же сервисе для заказчика оптимизировать время строительных и электромонтажных работ, уменьшать стоимость логистики и ускорять возведение объектов.
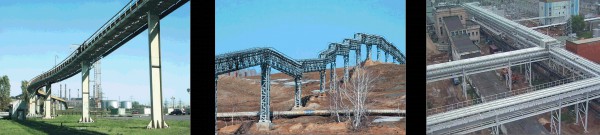
Кабельные эстакады находят широкое применение на различных крупных промышленных, металлургических и химических предприятиях, где территория крайне насыщенна различными коммуникациями и подземный вид прокладки кабеля затруднен, а также на предприятиях нефтегазодобывающей или перерабатывающей отрасли, перекачивающих станциях, на терминалах по хранению и перевалке нефтепродуктов. Зачастую в сложных климатических и коррозионно-агрессивных атмосферных условиях. Именно для таких компаний «ПРОкабель» разработала решение кабельных эстакад СЭММ по аналогии с самонесущими изолированными проводами, которые за счет своих технических преимуществ, простоты монтажа, универсальности в прокладке, а теперь еще и цены, буквально за несколько лет вытеснили с российского рынка неизолированные провода.
Каталог кабельных эстакад СЭММ «ПРОкабель» предназначен для главных инженеров, энергетиков крупных и средних производственных предприятий, электротехнических отделов проектных институтов, директоров и главных инженеров, энергетиков электромонтажных предприятий, а так же для всех, кто интересуется новыми решениями в возведении непроходных легких и средних кабельных эстакад.
1. Общие положения и термины. Выдержки из ПУЭ.
Кабельной эстакадой называется надземное или наземное открытое горизонтальное или наклонное протяженное кабельное сооружение. Кабельная эстакада может быть проходной или непроходной. Сооружают два вида кабельных эстакад:
• непроходная (с возможностью обслуживания со специально оборудованного автомобиля) и
• проходная — с площадками обслуживания. Оба вида эстакад предусматривают прокладку более 20 условных кабелей (согласно ПУЭ).
Кабельной галереей называется надземное или наземное закрытое полностью или частично (например, без боковых стен) горизонтальное или наклонное протяженное проходное кабельное сооружение. Сооружают три вида кабельных галерей: односторонняя — на 27 условных кабелей; двусторонняя — на 54; трехстенная — на 108 условных кабелей (рис. 1).
Кабельные эстакады и галереи применяют для прокладки силовых кабелей, идущих в одном направлении, в них прокладывают межцеховые электрические сети до 35 кВ. Под условными кабелями подразумевают силовые медные кабели сечением 3x240 мм2, поэтому при прокладке кабелей других сечений емкость сооружений может измениться. Сейчас непроходные эстакады стали использовать для прокладки кабеля с изоляцией из сшитого полиэтилена классом напряжения 110 кВ и выше, для питания подстанционных сооружений крупных промышленных предприятий.
Непроходные эстакады сооружают из железобетона или металла. Проходные эстакады и все виды галерей выполняют трех типов: железобетонные, металлические и комбинированные. Последние одновременно имеют железобетонные и металлические конструкции. Наружные кабельные эстакады и галереи должны иметь основные несущие строительные конструкции (колонны, балки) из железобетона с пределом огнестойкости не менее 0,75 ч или из стального проката с пределом огнестойкости не менее 0,25 ч. (пункт ПУЭ 2.3.113). Все металлические конструкции рассматриваемых кабельных сооружений в зависимости от среды, в которой они эксплуатируются, имеют соответствующее противокоррозионное или химически стойкое покрытие.
Наряду со специальными, предназначенными только для прокладки кабелей, эстакады бывают технологическими, на которых осуществляется совместное размещение (на разных уровнях) технологических трубопроводов и кабелей. При этом кабели прокладывают по возможности со стороны трубопроводов с негорючими веществами, а также ниже или выше трубопроводов в зависимости от плотности паров или газов в них.
Кабельные эстакады и галереи.
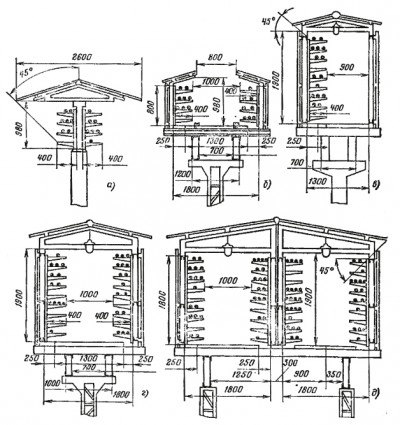
Рис. 1. Кабельные эстакады и галереи:
а — непроходная эстакада; 6 — проходная эстакада; в — односторонняя галерея; г — двусторонняя галерея; в — трехстенная комбинированная галерея
Все типы эстакад и галерей располагают на колоннах от 6 до 12 м. На переходах и поворотах трасс иногда выполняют нестандартные пролеты. Основная высота сооружения эстакад и галерей составляет 5 м от полотна автодороги. На территориях, где отсутствуют пересечения с дорогами или их число невелико, принимают высоту от планировочной отметки земли 2,5 м с переходами в местах пересечения с дорогами на другую высоту.
На переходах в проходных сооружениях выполняют пандус с уклоном не более 15°. Как исключение, устраивают лестницы с уклоном 1:1. При параллельном расположении и в местах пересечения кабельных эстакад и галерей с другими инженерными сооружениями наименьшие расстояния принимают в соответствии с данными, приведенными в табл. 1. Пересечение этих сооружений, кроме того, осуществляют под углом не менее 30°.Кабельныеэстакады и галереи отделяют от других помещений и соседних кабельных сооружений несгораемыми перегородками.
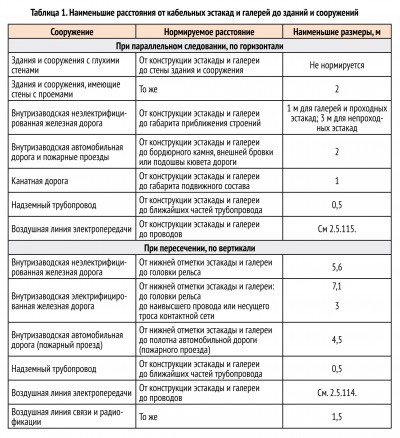
Раньше кабели, проложенные на эстакадах, защищались от прямых солнечных лучей солнцезащитными панелями (козырьками). Исключение составляли районы на территории России, расположенные севернее 65-й параллели, где такая защита не требовалась. В настоящее время, практически все кабельные заводы выпускают кабели стойкие к солнечному излучению, кроме кабелей предназначенных для внутренней прокладки. В настоящее время новый ГОСТ 31565-2012 регламентирует применение кабелей для прокладки в открытых кабельных сооружениях (эстакадах, галереях) с индексом – НГ (класс пожаробезопасности П1а.8.2.5.4.). Некоторые предприятия для унификации используют универсальный тип кабеля с индексом НГ-LS (класс пожаробезопасности
П1а.8.2.2.2) для прокладки по подстанциям и в закрытых кабельных сооружениях. Для уменьшения взаимных межфазных влияний, механических повреждений при токах КЗ, нагрева экранов, возникающих в одножильных кабелях свыше 6кВ, опытные проектировщики рекомендуют использовать трехжильные кабели. Такое решение позволяет уменьшить металлоемкость кабельной эстакады с помощью выбора лотков и полок меньшей ширины.
В кабельных сооружениях кабели рекомендуется прокладывать целыми строительными длинами, а размещение кабелей в сооружениях должно производиться в соответствии со следующим правилам:
1. Контрольные кабели и кабели связи следует размещать только под или только над силовыми кабелями;
при этом их следует отделять перегородкой. В местах пересечения и ответвления допускается прокладка контрольных кабелей и кабелей связи над и под силовыми кабелями.
2. Контрольные кабели допускается прокладывать рядом с силовыми кабелями до 1 кВ.
3. Силовые кабели до 1 кВ рекомендуется прокладывать над кабелями выше 1 кВ; при этом их следует отделять перегородкой.
4. Различные группы кабелей: рабочие и резервные кабели выше 1 кВ генераторов, трансформаторов и т. п., питающие электроприемники I категории, рекомендуется прокладывать на разных горизонтальных уровнях и разделять перегородками.
5. Разделительные перегородки, указанные в пп. 1, 3 и 4, должны быть несгораемыми с пределом огнестойкости не менее 0,25 ч. При применении автоматического пожаротушения с использованием воздушно-механической пены или распыленной воды перегородки, указанные в пп. 1, 3 и 4, допускается не устанавливать.
6. На наружных кабельных эстакадах и в наружных закрытых частично кабельных галереях установка разделительных перегородок, указанных в пп. 1, 3 и 4, не требуется.
При этом взаимно резервирующие силовые кабельные линии (за исключением линий к электроприемникам особой группы I категории) следует прокладывать с расстоянием между ними не менее 600 мм и рекомендуется располагать: на эстакадах по обе стороны пролетной несущей конструкции (балки, фермы); в галереях по разным сторонам от прохода (пункт ПУЭ 2.3.120).
Прокладка контрольных кабелей допускается пучками на лотках и многослойно в металлических коробах при соблюдении следующих условий (пункт ПУЭ 2.3.124):
1. Наружный диаметр пучка кабелей должен быть не более 100 мм.
2. Высота слоев в одном коробе не должна превышать 150 мм.
3. В пучках и многослойно должны прокладываться только кабели с однотипными оболочками.
4. Крепление кабелей в пучках, многослойно в коробах, пучков кабелей к лоткам следует выполнять так, чтобы была предотвращена деформация оболочек кабелей под действием собственного веса и устройств крепления.
5. В каждом направлении кабельной трассы следует предусматривать запас емкости не менее 15 % общей емкости коробов.
Прокладка силовых кабелей пучками и многослойно не допускается.
В кабельных сооружениях прокладку контрольных кабелей и силовых кабелей сечением 25 мм2 и более, за исключением небронированных кабелей со свинцовой оболочкой, следует выполнять по кабельным конструкциям (консолям). Контрольные небронированные кабели, силовые небронированные кабели со свинцовой оболочкой и небронированные силовые кабели всех исполнений сечением 16 мм2 и менее следует прокладывать по лоткам или перегородкам (сплошным или несплошным) (пункт ПУЭ 2.3.123).
Выше названный пункт ПУЭ не исключает прокладку кабелей сечением свыше 25 мм2 по лестничным лоткам, а регламентирует расстояние между опорными конструкциями для крепления кабелей на разные классы напряжения. Это расстояние определяет установку кабельных зажимов для классов напряжений свыше 10 кВ, т.к. у данных кабелей в момент межфазного короткого замыкания возникают большие динамические нагрузки на элементы конструкций и их крепления.
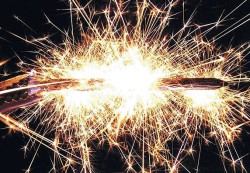
Формула для определения силы воздействия на кабельные хомуты в зависимости от расстояния при креплении кабеля:
Где: F – сила воздействия при коротком замыкании (Ньютонах), l – расстояние между зажимами в метрах,
Is – максимальный ток короткого замыкания, исходя из сечения экрана кабеля в кА, a – межосевое расстояние между кабелями в сантиметрах.
*Токи короткого замыкания рассчитаны при температуре жилы до начала короткого замыкания 90°С и предельной температуре жилы при коротком замыкании 250°С.
Для других значений сечения медного экрана допустимый ток односекундного короткого замыкания рассчитывают по формуле:
Iк.з.= 0,203 х Sэкр., где
Iк.з. - допустимый ток односекундного короткого замыкания в медном экране, кА;
Sэкр. - номинальное сечение медного экрана, мм2.
Для продолжительности короткого замыкания, отличающейся от 1 с, значения тока короткого замыкания, указанные в таблицах 5 и 6, необходимо умножить на поправочный коэффициент К, рассчитанный по формуле:
В наше время, частое использование одно- и многожильных кабелей свыше 6 кВ из полимерной изоляции и диаметром по оболочке свыше 30 мм накладывает дополнительные требования на некоторые элементы кабельных эстакад:
• Кабели, проложенные в одной плоскости на воздухе в кабельных сооружениях (на лотках, консолях и т.д.) должны быть закреплены в местах, расположенных по длине кабельной трассы с шагом от 1 до 1,5 метров (Инструкция NEXANS/6-35/04).
• Номинальный ток у большинства производителей указывается исходя из расстояния между кабелями:
• для одножильных кабелей токи рассчитаны при прокладке в треугольнике – вплотную.
• При прокладке в плоскости – при расстоянии между кабелями в свету, равном диаметру кабеля.
• Минимальный радиус изгиба кабеля при прокладке должен быть не менее 15 диаметров по внешней оболочке для одножильных кабелей и 12 диаметров по внешней оболочке для трехжильных кабелей, 7,5 диаметров по внешней оболочке с использованием специальных шаблонов. (ГОСТ-Р 55025-2012. «Кабели силовые с пластмассовой изоляцией на номинальное напряжение от 6 до 35 кВ включительно. Общие технические условия»).
• Число соединительных муфт на 1 км вновь строящихся кабельных линий должно быть не более: для трехжильных кабелей 1- 10 кВ сечением до 3 х 95 мм2 - 4 шт.; для трехжильных кабелей 1-10 кВ сечениями 3 х 120 - 3 х 240 мм2 - 5 шт.; для трехфазных кабелей 20-35 кВ - 6 шт.; для одножильных кабелей 2 шт. (ПУЭ 2.3.70.)
• Для кабельных линий 110-220 кВ число соединительных муфт определяется проектом. Кабели, прокладываемые по конструкциям, консолям, эстакадам, стенам, перекрытиям, фермам и т.д., следует закреплять в конечных точках, непосредственно у концевых муфт в двух местах, у соединительных муфт, на поворотах трассы (с обеих сторон от изгиба на расстоянии не более 0,5 м), на остальных участках трассы – в местах, расположенных по длине кабельной линии с шагом от 1 до 1,5 м. (Руководство, по выбору, прокладке, монтажу, испытаниям и эксплуатации кабелей с изоляцией из сшитого полиэтилена на напряжение 64/110 кВ. ЗАО Завод «Южкабель»)
• Кабели, прокладываемые вертикально по конструкциям и стенам, должны быть закреплены на каждой кабельной конструкции. Крепление кабелей должно быть выполнено таким образом, чтобы была предотвращена деформация кабелей и муфт под действием собственного веса кабеля, а также в результате действия механических напряжений, возникающих при циклах нагрева и охлаждения и при магнитных взаимодействиях во время коротких замыканий. (Руководство, по выбору, прокладке, монтажу, испытаниям и эксплуатации кабелей с изоляцией из сшитого полиэтилена на напряжение 64/110 кВ. ЗАО Завод «Южкабель»)
• Для компенсации температурных расширений металлических конструкций кабельной эстакады кабели должны укладываться «змейкой» в местах их соединений.
2. Виды покрытий для несущих конструкций кабельных эстакад
Незащищенная сталь в атмосфере, воде и почве подвержена коррозии, что может привести к ее повреждению. Поэтому, чтобы избежать коррозионного повреждения, стальные конструкции обычно защищаются, чтобы противостоять коррозионному напряжению в течение срока действия этой конструкции.
В советское время все эстакады и галереи изготавливались из черного металла и по факту завершения строительной части, обрабатывались грунтом или покрывались краской. Такое решение принималось исходя из срока службы 5-10 лет, а далее периодическое обновление покрытий на протяжении всего срока эксплуатации. Это решение было материалоемким, а значительная толщина стали позволяла увеличивать срок службы за счет «ухода» металла. В нашей стране действующим является ГОСТ 15150-69 «Машины, приборы и другие технические изделия. Исполнения для различных климатических районов. Категории, условия эксплуатации, хранения и транспортирования в части воздействия климатических факторов внешней среды». В ракурсе рассматриваемой темы стандарт регламентирует типы атмосферы исходя из содержания коррозионно-активных агентов и нормы воздействия механической пыли, очень схожие со стандартом ISO, поэтому, чтобы более полно оценить и понять разницу применяемых покрытий, рассмотрим определения и термины из стандарта ISO 12944 действующий на территории Российской Федерации.
2.1. Термины стандарта ISO 12944.
1. Коррозионность: способность окружающей среды, вызвать коррозию в данной коррозионной системе. [Стандарт ISO 8044]
2. Коррозионное напряжение: фактор окружающей среды, который способствует коррозии.
3. Коррозионная система: система, состоящая из одного или более металлов и все факторы окружающей среды, которые влияют на коррозию. [Стандарт ISO 8044]
4. Климат: погода, преобладающая на данной местности или данной территории, как установлено статистически метеорологическими параметрами, зарегистрированными в течение длительного периода.
5. Атмосфера: смесь газов, также аэрозолей и частиц, которые окружают данный объект.
6. Атмосферная коррозия: коррозия в атмосфере Земли при окружающих температурах. [Стандарт ISO 8044]
7. Тип атмосферы: характеристика атмосферы на основе присутствия коррозийных элементов и их концентрация.
ПРИМЕЧАНИЕ - главные коррозийные элементы - газы (особенно диоксид серы) и соли (особенно хлориды и сульфаты).
7.1. Сельская атмосфера: атмосфера, преобладающая в сельских районах, маленьких городах, без значительного загрязнения коррозийными элементами, такими, как диоксида серы или хлорид.
7.2. Городская атмосфера: загрязненная атмосфера, преобладающая в густонаселенных территориях без значительной концентрации промышленности. Имеет среднюю концентрацию загрязнения, такую, как диоксид серы или хлорид.
7.3. Промышленная атмосфера: атмосфера, загрязненная коррозионными загрязнителями от местной
и региональной промышленностей (в основном диоксид серы).
7.4. Морская атмосфера: атмосфера в озере или на море.
ПРИМЕЧАНИЕ - морская атмосфера может распространяться на некоторое расстояние, в глубь территории в зависимости от топографии и преобладающего направления ветра. Обычно эта атмосфера загрязнена аэрозолями морских солей (в основном хлориды).
8. Местная окружающая среда: атмосферные условия, преобладающие вокруг основных элементов конструкции.
ПРИМЕЧАНИЕ - Эти условия определяют категорию коррозионности и включают метеорологические параметры, и параметры загрязнения.
9. Микро-окружающая среда: среда на границе между составляющими элементами конструкции и его окружением. Микросреда - один из решающих факторов в оценке коррозионного напряжения.
10. Период влажности: период времени, в течение которого металлическая поверхность покрыта пленкой электролита, которая способна вызвать атмосферную коррозию. Период влажности может быть рассчитан исходя из температуры и относительной влажности, суммируя время, в течение которого относительная влажность была около 80 % и, в то же время, температура около 0 °C.
2.2. Необходимые выдержки из стандарта ISO 12944
Атмосферная коррозия - процесс, который происходит при наличии влажного слоя на металлической поверхности.
Влажный слой может быть настолько тонок, что он невидим для невооруженного глаза.
Темп коррозии увеличивается из-за следующих факторов:
- увеличение относительной влажности;
- выпадение конденсации (когда температура поверхности ниже точки выпадения росы);
- увеличение количества загрязнения в атмосфере (коррозийные загрязнители могут реагировать со сталью и могут формировать отложения на поверхности).
Для целей ISO 12944, атмосферная среда разделяется на шесть атмосферно - коррозионных категорий:
Для определения категории коррозионности, рекомендуется испытание стандартных образцов.
Таблица 5 определяет категорию коррозионности при потере массы или толщины стандартных образцов, изготовленных из низкоуглеродистой стали или цинка, после первого года действия. Для детализации стандартных образцов и обращения с ними до и после их выставления, см. ISO 9226. Экстраполяция потерь массы и толщины за период менее одного года или наоборот за более длительный период времени, не даст надежных результатов и поэтому, не разрешается. Потеря массы или толщины, полученные от образцовой стали и цинка иногда могут дать различные категории. В таких случаях, берется более высокая категория коррозионности.
Обычно, по типу климата можно сделать только общие заключения о коррозии. В холодном или сухом климате уровень коррозии будет ниже, чем в умеренном климате; самым высоким уровнем коррозии будет в жарком и влажном климатах, а также в морском климате, хотя могут быть значительные местные отклонения.
Главной проблемой может быть период времени, в течение которого конструкция подвергается высокой влажности, это также называют временем влажности (Таблица 6).
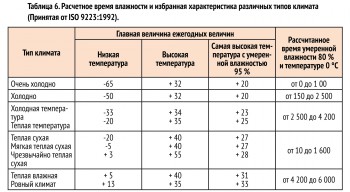
Коррозионное воздействие на стальные конструкции, расположенные внутри помещений и защищенные от окружающей, среды обычно незначительны. Если внутренняя часть здания только частично защищена от окружающей среды, тогда воздействие коррозии может быть оценено, как такое же, что ассоциируется с типом атмосферы, окружающей это здание.
Эффект коррозионного воздействия, вызванный климатом внутри этого помещения, может быть усилен тем, как это помещение использовалось, и к этому воздействию нужно относится как к особому случаю. Такое воздействие обычно происходит в закрытых плавательных бассейнах с хлорированной водой, помещениях, где обитают домашние животные и других зданиях специального назначения. Более охлажденные участки на конструкциях могут быть подвержены более высокому коррозионному воздействию в результате сезонного образования конденсата. В случаях, когда поверхность увлажняется электролитами, даже если такое увлажнение только временное (например, пропитанные строительные материалы), необходимы особенно строгие коррозионные требования.
Коррозия значительно усиливается из-за загрязнителей, появляющихся в результате работы завода (например, кислот, щелочей или солей, органических растворителей, агрессивных газов и частиц пыли). Такое воздействие может происходить вблизи коксохимических заводов, травильных цехов, гальванических заводов, лакокрасочных заводов, деревообрабатывающих заводов, кожевенных заводов и нефтеперерабатывающих предприятий.
2.3. Применяемые виды покрытий.
С вопросом покрытия изделий для улучшения их эксплуатационных характеристик человечество столкнулось давно. Использовали сало и кровь животных для покрытия деревянных изделий, различные смолы и масла деревьев и растений. С появлением железа увеличилась необходимость в разработке покрытий и для него. Первые стали были высокоуглеродистыми и ржавели очень слабо. Подобные образцы изделий можно встретить повсеместно по всему миру и удостовериться в этом (например, в Невьянской башне около железоделательного завода знаменитых уральских металлургов Демидовых в Невьянске, Свердловской области). Далее для удешевления и ускорения технологий производства металла понадобилось добавление различных сторонних примесей металлов и использование конвертерного метода его плавки, что и вызвало изменение коррозионных свойств металла. Конечно, в дальнейшем это потребовало создания более простого и дешевого способа его защиты.
2.3.1. Подготовка поверхности
Подготовка поверхности — начальная стадия процесса получения покрытия — в значительной степени определяет коррозионную стойкость изделий и, соответственно, долговечность покрытия. При нанесении по плохо подготовленной поверхности (зажиренной, имеющей окалину, ржавчину и т.п.) наблюдается быстрое отслаивание покрытия, как на небольших участках, так и по всей поверхности. Наличие загрязнений на поверхности под слоем защиты может приводить к возникновению многочисленных очагов коррозии и последующему разрушению покрытия. Из всего многообразия встречающихся загрязнений, подлежащих удалению с поверхности, можно выделить следующие:
• органические загрязнения — антикоррозионные смазки и смазочные масла, в состав которых входят минеральные масла, вазелин, нефтяной воск, парафины, жирные кислоты, канифоль, древесные смолы и др.;
• неорганические загрязнения — нагары и окислы, образующиеся в результате операций предварительной обработки, окалина, ржавчина, металлическая стружка и другие крупные и мелкие неорганические частицы, смешанные со смазкой, остающейся после механической обработки и др.;
• смешанные загрязнения — смазки, применяемые при обработке металлов давлением, специальные смазки и эмульсионные композиции, в состав которых входят различные пигменты в виде тонкоизмельченных порошков и т.п.;
Поверхность изделий не должна иметь заусенцев, острых кромок (радиусом менее 0,3 мм), сварочных брызг, наплывов пайки, прожогов, остатков флюса (поверхность литых изделий не должна иметь неметаллических макровключений, пригаров, нарушений в виде раковин, трещин, спаев, неровностей и т. п.);
Она должна быть сухой, обеспыленной, без загрязнений маслами или смазками, не иметь окалины и следов ржавчины, а также налетов вторичной ржавчины, образующейся в процессе обработки изделий из черныхиметаллов.
При удалении загрязнений с поверхности изделий особенно важен выбор наиболее эффективного метода обработки и составов, применяемых для этой цели. Они определяются:
1. Материалом обрабатываемой поверхности;
2. Видом и степенью загрязнения;
3. Требованиями к условиям и срокам эксплуатации.
В зависимости от производственных условий, размеров изделий, их количества обработка поверхности химическими методами может производиться погружением изделий в ванну с раствором или подачей на них раствора под давлением через специальные форсунки (струйная обработка). В последнем случае эффективность обработки повышается, так как к физико-химическому воздействию на обрабатываемую поверхность добавляется механическое при этом к поверхности непрерывно подается незагрязненный раствор.
Для обработки поверхности изделий перед нанесением различных видов грунта, красок и порошковой краски используется обезжиривание, удаление окисных пленок (абразивная очистка, травление), нанесение конверсионного слоя (фосфатирование, хромагирование, пассивирование). Первая операция является обязательной, остальные применяются в зависимости от конкретных условий и требований.
Обезжиривание — удаление с поверхности жировых загрязнений, следов пота, солей, шлама и т.п. под воздействием специальных химических веществ (органических растворителей, щелочных водных и эмульсионных составов). Обезжиривание органическими растворителями (уайт-спирит, нефрас 150/200, бензин БР-1 с антистатической добавкой) является наиболее простым методом, В этом случае поверхность изделия протирается чистой ветошью или волосяными щетками, смоченными растворителем. Затем их протирают сухой чистой салфеткой или обдувают сжатым воздухом. Вместо протирки (в зависимости от размеров изделий) можно использовать их промывку в двух—трех ваннах с налитым в них растворителем. Применение растворителей характеризуется высокой скоростью их проникновения в загрязнения и удаления последних, быстрым испарением с изделий их избытка, нейтральным остатком на поверхности. К недостаткам их применения можно отнести относительно высокую стоимость, пожароопасность, токсичность, низкое качество очистки (после испарения растворителя на поверхности остаются следы загрязнений).
Обезжиривание щелочными водными составами. Наибольшее распространение получили составы типа КМ, представляющие собой слабо- или среднещелочные бессиликатные моющие средства. Они состоят из смеси солей ортофосфорной, борной и других кислот с добавкой поверхностно-активных веществ, обеспечивающих стабильное моющее действие, пониженное пенообразование и уменьшенный расход моющих средств. Составы (КМ-1, КМ-17, КМ-18, КМ-19, КМ-21, КМ-22, КМ-25 и др.) изготавливаются «Экохиммаш» (Буй, Костромской обл.) и поставляются в виде порошков белого или желтовато-белого цвета, готовых к употреблению. Их растворяют в
технической воде при непрерывном перемешивании. Время обработки изделий 5—15 мин при 60—70 °С. Выбор моющих составов и их расход зависит от вида загрязнения, материала изделия, способа обезжиривания, вида производства и составляет ориентировочно 0,2—1,0 кг/м2. Составы не воспламеняются, экономичны, малотоксичны, поддаются регенерации. К недостаткам их применения можно отнести большее время очистки, необходимость механического перемешивания и подогрева состава, чрезмерное ценообразование. После обезжиривания щелочными водными составами обработанную поверхность необходимо тщательно промыть. Рекомендуется
промывка в теплой воде при температуре 20—40 °С.
Эмульсионное обезжиривание — комбинированный способ, сочетающий достоинства применения органических растворителей и щелочных водных составов. Эмульсионные составы представляют собой эмульсии растворителей в воде, стабилизированные поверхностно-активными веществами. Подобные составы обладают высокой растворяющей, смачивающей и эмульгирующей способностью, поэтому в процессе эмульсионной очистки с металлической поверхности полностью удаляются различные масла, смазки и неорганические загрязнения.
При очистке эмульсионными составами время очистки по сравнению с обезжириванием в щелочных составах сокращается, однако требуется более тщательная промывка. Эмульсионное обезжиривание можно осуществлять при комнатной температуре без ухудшения качества очистки поверхности. Эмульсионные составы применяют при наличии оборудования для нейтрализации и обезвреживания отработанных составов. В связи с этим их использование ограничено.
Обычно горячему цинкованию подвергают изделия из углеродистых и низколегированных сталей. Поверхность таких изделий обычно покрыта ржавчиной и окалиной.
Ржавчина (условно можно выразить формулой Foe • Fe2 O3 • nH2O) образуется на стальных изделиях в кислородсодержащей среде в присутствии влаги при комнатной температуре. Вначале на поверхности стали во влажной атмосфере образуется гидрат закиси железа Fe(OH)2 , который в дальнейшем окисляется кислородом.
Вследствие губчатого строения и наличия многочисленных капилляров ржавчина затрудняет обезжиривание поверхности стали.
Окалина на стальных изделиях обычно образуется в процессе их изготовления (например, при горячей прокатке, прессовании) или последующей термической обработки. В отличие от ржавчины окалина образуется при повышенных температурах (400 °С и выше). Состав, строение, толщина, равномерность распределения окалины по поверхности изделия зависит от многих факторов (например, состава стали, температуры и продолжительности окисления, содержания кислорода в окружающей среде). В основном окалина состоит из оксидов железа, близких по составу к FeO (вюстит), Fe3 O4 (магнетит), Fe2 O3 (гематит). Непосредственно на стали находится вюстит, затем располагаются магнетит и гематит. Вюстит имеет пористое строение и низкую прочность, магнетит и гематит, наоборот, обладают высокой прочностью и плотным строением. Следует отметить, что окалина с трехслойным строением образуется на стали при температуре выше 570 °С при избытке кислорода в атмосфереи достаточно быстром охлаждении до низких температур. В других случаях окалина состоит из двух или одного слоя. Чаще всего слои FeO—Fe3 O4 — Fe2 O3 взаимно проникают друг в друга. Обычно на стали образуется многокомпонентная сложного состава окалина, которая является результатом окисления не только железа, но и присутствующих в стали различных примесей (Mn, Si, P, S, N1, Сг, Си и др.). Примеси в окалине находятся либо в виде металлических включений (например, Ni, Си), либо в виде оксидов.
Окалина на кремнистых сталях существенно отличается от окалины, образующейся на углеродистых и нержавеющих сталях. В процессе термической обработки кремнистых сталей в окислительных средах наряду с внешним окислением происходит процесс внутреннего окисления стали. В слое, в котором происходит внутреннее окисление, появляются вкрапления двуокиси кремния. Под этим слоем находится обезуглероженный слой чистого феррита. Внешний слой окалины состоит из вюстита с вкраплениями магнетита. Таким образом, наличие в составе окалины кремнистых сталей большой доли чистого феррита и инертного кремнезема определяет осо-
бенности ее травления. При прокатке образуется, в основном, вюстит, который сравнительно легко растворяется в кислоте; при отжиге листов образуются гематит и магнетит — труднорастворимые при травлении. Следовательно, наилучшей сталью для оцинкования является холоднокатаная. Следует отметить, что особенно разнообразная по толщине, структуре и составу окалина может возникать на трубах, что обусловлено условиями их производства.
Удаление ржавчины и окалины можно производить химическим и механическим методами.
Химический метод (травление) получил широкое распространение при подготовке поверхности изделий перед горячим цинкованием. Обычно травлением удаляют ржавчину и окалину с поверхности листов, полосы, труб, проволоки и других стальных изделий при подготовке их к цинкованию. На практике для травления изделий из углеродистых и низколегированных сталей широко применяют 18— 22 %-ные водные растворы серной кислоты или 20— 25 %-ные водные растворы соляной кислоты.
Сравнивая достоинства и недостатки травильных растворов на основе серной и соляной кислот, следует отметить, что при травлении в серной кислоте растворяется не более 15—20 % окалины, в соляной до 40—50 %. Поверхность стали после травления в растворах соляной кислоты получается более гладкой, кислоте из-за «перетрава» поверхности стали нельзя проводить без ингибиторов (замедлителей) кислотной коррозии. В этой связи необходимо отметить что с появлением надежных ингибиторов кислотной коррозии (ПКУ, ХОСП-10, БА-6, И-1-В и др.) достаточно хорошее качество поверхности достигается как при травлении в солянокислых, так и при травлении в сернокислых растворах. Выбор типа травильного раствора обусловлен в основном технико-экономическими соображениями. Перспективно применение травильных растворов, содержащих смеси серной и соляной кислот.
Очистку стальной поверхности от ржавчины и окалины можно производить и механическим методом. Наиболее широко применяют дробеструйный или дробеметный способы, которые обеспечивают качественную подготовку поверхности стальных изделий.
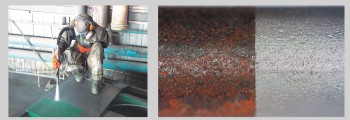
После травления изделия промывают в воде для удаления с их поверхности остатков травильного раствора и солей железа. Состав железа на поверхности стальных изделий может достигать 3—3,2 г/м2 после сернокислотного и 2—2,5 г/м2 после солянокислого травления в зависимости от концентрации и вязкости травильного раствора. Поэтому промывку изделий после сернокислотного травления желательно проводить сначала в горячей (60 °С) воде, а затем — в холодной. Если необходимо смыть остатки травильного шлама, применяют промывку из брандспойта или струйное промывание водой под давлением более 4-105 Па. Учитывая, что после травления в соляной кислоте на поверхности стали остается примерно в 1,5 раза меньше солей железа, а также, что железные соли соляной кислоты смываются с протравленной поверхности значительно лучше, чем соли серной кислоты, производят обработку изделий в водном растворе соляной кислоты (50 г/л) при 18— 20 °С (например, при цинковании труб). Эту операцию называют декапированием или подтравливанием. При этом происходит переход сульфата железа в хлорид: FeSO4 + 2HClFeCl2 f H2 SO4 .
Затем изделия промывают в холодной проточной воде.
При промывании полосы и проволоки применяют струйно-возвратный и эффективный струйный способы. Иногда для улучшения очистки промывание проводят в щеточно-моечных машинах. Предельное содержание примесей в промывной воде зависит от их свойств. Если эти примеси не образуют нерастворимых соединений с рабочим раствором, то их содержание может достигать 3—5 г/л. В противоположном случае концентрация нерастворимых соединений должна быть ниже предела растворимости.
Хорошо протравленные и промытые изделия поступают на заключительную подготовительную операцию — флюсование. Ее проводят для удаления солей и оксидов металлов с поверхности цинкуемого изделия, а также с поверхности расплавленного цинка в месте погружения изделия и, кроме того, для улучшения смачивания поверхности изделия расплавленным цинком путем снижения поверхностного натяжения расплава цинка. Летучие соединения, образующиеся при разложении флюса, способствуют механическому удалению загрязнений на зеркале ванны и создают нейтральную атмосферу в месте погружения изделий в расплав цинка.
В качестве флюса при цинковании в расплаве чаще всего используют смесь из солей хлористого аммония (NH4 C1) я хлористого цинка (ZnCl2). Основную роль в таком флюсе играет хлористый аммоний, так как он является поставщиком газообразных хлоридов, образующихся при разложении NH4CI при контакте с расплавленным цинком. Эта реакция идет в присутствии влаги, которая в большем или меньшем количестве всегда присутствует на изделиях. Влага способствует разложению хлористых солей с образованием активной соляной кислоты. Хлористый водород взаимодействует с оксидом железа, цинка и других элементов, присутствующих на поверхности
изделий и на зеркале ванны:
FeO + 2HCl--FeCl2 + H2O,
ZnO + 2HCl--ZnCl2 + Н2О.
Большинство образующихся хлоридов (алюминия, олова, сурьмы, FeCl3) испаряются, так как имеют более низкую температуру кипения, чем температура расплава цинка. С хлоридом железа (FeCl2 ) связано образование гарт-цинка — нежелательного продукта процесса горячего цинкования. При контакте с расплавленным цинком FeCl2 восстанавливается до железа:
FeCl2 + Zn--Zn Cl2 + Fe.
Образовавшееся железо, взаимодействуя с жидким цинком, переходит в гартцинк, который осаждается на дно ванны цинкования. С увеличением количества железных солен резко увеличивается образование гартцинка. Это еще раз подтверждает необходимость хорошей промывки изделий после операций травления и декапирования.
В практике цинкования в расплаве цинка сложилось два основных процесса: «мокрый» способ цинкования и «сухой». В связи с этим и флюсовую обработку изделий выполняют двумя способами: в расплавленном флюсе или в водном растворе флюса с последующей его сушкой.
При «сухом» способе цинкования флюсовую обработку стальные изделия проходят в водном растворе флюса с последующей сушкой в специальных сушильных печах (сушилах). Основные составляющие водных растворов флюсования — хлорид цинка и хлорид аммония. Для повышения эффективности раствора флюсования в него добавляют различные поверхностно-активные вещества (например, ОП-7, ОП-10, сульфопонат). Растворы флюсования подогревают до 50—60 °С, что улучшает обработку изделий и способствует более быстрому высыханию флюса. Подогрев раствора обычно осуществляют паром, который пропускают через змеевик, уложенный на
дно ванны флюсования. В процессе заключительной стадии сушки флюса на поверхности изделий образуется равномерный высушенный слой флюса. При этом происходит подогрев изделий, что облегчает нагрев ванны оцинкования и улучшает технико-экономические показатели ее работы. Кроме того, образующаяся плотная пленка из солей предохраняет поверхность изделий от окисления до-погружения их в расплавленный цинк. Когда слой флюса достаточно высушен, исключаются всплески расплавленного цинка при погружении изделий в ванну цинкования.
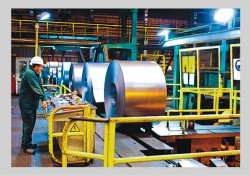
Особо следует остановиться на подготовке поверхности при цинковании полосы. Общая загрязненность поверхности полосовой стали в исходном состоянии может достигать 1800 мг/м2. Количество и вид загрязнений зависят от многих факторов, главными из которых являются условия горячей прокатки, травления, холодной прокатки, материал прокатной смазки. Загрязнения на поверхности холоднокатаной стали делятся на механические (продукты износа металла — металлическая пыль) и жировые (остатки прокатной смазки). Кроме того, при травлении горячекатаной стали образуются загрязнения в виде остатков солей железа неорганических кислот, например, FeCl3 FeSO4 , Fe2 (SO4 )3. Поверхность полос, отожженных в колпаковых печах, может иметь загрязнения от термического разложения смазки и остатки металлической пыли. После отжига полос непрерывным способом на их поверхности могут быть остатки сухих компонентов от моющих растворов, чаще всего содержащих гель кремниевой кислоты. Требования к чистоте поверхности полосовой стали перед цинкованием высоки и в соответствии с ними загрязненость должна быть менее 40 мг/м2.
Современные агрегаты непрерывного горячего цинкования оснащены необходимыми средствами для подготовки поверхности полосы. В зависимости от способа горячего цинкования и конструкций агрегатов применяют разные методы подготовки поверхности полосы.
• Химическая подготовка
Подготовка поверхности полосы с применением обезжиривающих растворов проводится по схеме: химическое и (или) электрохимическое обезжиривание, промывка и сушка. В настоящее время для обезжиривания поверхности полос в агрегатах оцинкования используют, в основном, щелочные растворы и иногда органические растворители. В качестве основных компонентов водных щелочных растворов применяют гидроксиды (NaOH, КОН), карбонаты ;(Na2 CO3 , СаСОз), фосфаты (Na3 PO4 , Na2 HPO4 , Na4 P2 O7 , Na2 H2 P2 O7 , Ка5 Рз0ю), силикаты (Na2 Si03 , Na2 Si2 05 ) и др. После электрохимического обезжиривания следует двухступенчатая струйная промывка полосы. Температура воды в ваннах промывки первой ступени 60—65, второй ступени 90—95 °С. Сушку полосы производят горячим (85— 90 °С) воздухом.
• Термическая подготовка.
Термическая подготовка поверхности полосы в агрегатах горячего цинкования, работающих по классическому способу Сендзимира идет путем окислительного нагрева до температуры 470-480 С. Образующаяся при этом тонкая окисная пленка восстанавливается при последующем отжиге в восстановительной атмосфере.
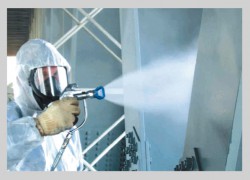
2.3.2. Грунтование ГФ-021.
Грунтовка ГФ-021 (ГОСТ 25129-82) — один из самых распространенных лакокрасочных материалов используемых в России, применя-
емых для окраски металлических, деревянных и других поверхностей. Популярность данного материала обусловлена, в первую очередь, универсальностью применения — для наружных и внутренних работ, и конечно, невысокой ценой, а так же широким выбором организаций-производителей. Данный материал можно приобрести как в промышленной таре, так и в небольших емкостях для розничной торговли.
Обеспечивая приемлемую адгезию и антикоррозионную защиту поверхности, грунт ГФ-021 рекомендуется перекрывать совместимыми эмалями, для получения комплексного покрытия. Грунтовку наносят на поверхность методом пневматического и безвоздушного распыления, распылением в электрополе, струйным обливом, окунанием, кистью. Перед применением грунтовку разбавляют до рабочей вязкости сольвентом, ксилолом, или смесью одного из указанных растворителей с уайт-спиритом (нефрас-СЧ-155/200) по ГОСТ 3134 в соотношении по массе 1:1. Для окраски изделий распылением в электрополе грунтовку разбавляют разбавителем РЭ-4В ГОСТ 18187.
Грунтовку ГФ-021, предназначенную для розничной торговли, можно разбавлять растворителями РС-2, 649,650. Грунтовку наносят кистью или краскораспылителем. Время высыхания однослойного покрытия при 20±2°C –24 часа. Окрашиваемая поверхность должна быть очищена от ржавчины, окалины, загрязнения и обезжирена, должна быть сухой.
Данное покрытие в виду своей дешевизны и механической стойкости хорошо подходит во временных сооружениях (например, калийные шахты до начала их выработки, временные эстакады для строительных площадок) срок эксплуатации которых не превышает 5 лет.
Изделия покрытые грунтом соответствуют климатическим исполнениям УХЛ3, У3. Используются для типов атмосферы I по ГОСТ 15150-69 (категория коррозионности С1-С2)
2.3.3. Порошковое покрытие.
Серийное производство порошковых красок в СССР (на Ярославском ЛКЗ) было начато только в 1975 г. Сейчас это одно из самых популярных защитных покрытий, т.к. используется во всех видах народного хозяйства, начиная от производства бытовой и автомобильной техники, заканчивая дверьми и кровельными материалами. Широким распространением порошковые краски (особенно термоотверждаемые на основе эпоксидных, полиэфирных смол и полиуретанов) обязаны, прежде всего тому, что они не содержат растворителей и на 100 % состоят из веществ, которые при отвержении превращаются в тонкослойное, практически непроницаемое для влаги, кислорода, кислот, солей и других химических веществ высокопрочное и твердое абразивостойкое покрытие со сроком службы, превышающим порой срок службы окрашенного изделия.
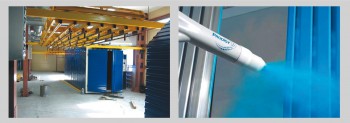
Существуют различные способы получения покрытия на основе порошковой краски. Однако ниже будет рассматриваться лишь наиболее распространенный процесс с использованием на стадии нанесения на изделие электростатически заряженной порошковой краски, распыляемой специальным пневматическим распылителем (пистолетом-распылителем) и удерживаемой
на поверхности заземленного окрашиваемого изделия силой электростатического притяжения. Процесс осуществляется в камерах нанесения, которые оснащены системами отсоса воздуха для предотвращения попадания порошковой краски в помещение и совмещенными с ними системами улавливания прошедшей мимо окрашиваемого изделия порошковой краски для возврата ее в процесс и утилизации или обезвреживания.
Пистолеты-распылители с питателями составляют установку (агрегат) нанесения порошковой краски, обеспечивающую получение смеси порошковой краски с воздухом, образование факела и приобретение частицами порошковой краски электрического заряда. Вылетающая из пистолета заряженная порошковая краска образует факел той или иной формы в зависимости от применяемого сопла (насадки) пистолета, движется под влиянием струй воздуха в факеле и силы электрического притяжения к заземленной окрашиваемой детали и оседает на ее поверхности, удерживаясь теми же силами электрического притяжения.
Применяют два способа заряда частиц: коронирующим электродом, находящимся под высоким напряжением, и с использованием «трибоэффекта», т.е. эффекта приобретения разноименных зарядов соприкасающимися телами, изготовленными из разных материалов .
При первом способе применяется подвод высокого (20—100 тыс. В) постоянного по знаку напряжения к коронирующему электроду от специального генератора высокого напряжения, располагающегося в зависимости от конструкции внутри пистолета или вне его. В случае ручных пистолетов следует отдавать предпочтение генераторам, встроенным в пистолет, так как при этом обеспечивается более высокая безопасность работника (подвод к пистолету безопасного напряжения от 9 до 30 В в зависимости от модели) и исключается необходимость подсоединения к пистолету высоковольтного кабеля, более жесткого и тяжелого по сравнению с низковольтным,
что вызывает повышенную утомляемость работающего.
При втором способе зарядки частиц ствол и другие детали пистолета, с которыми соприкасается порошковая краска, изготавливается из специального материала (обычно фторопласта — для эпоксисодержащих порошковых красок).
На конвейерных линиях при малой частоте движения распылителей на траверсе по сравнению со скоростью движения изделия на конвейере в сочетании с узким или неравномерным факелом возможно получение разнотолщинного покрытия в виде чередующихся полос (волн) — следов относительного движения факела и изделия. Такой же дефект может быть и при ручном нанесении порошковой краски из-за недостаточной квалификации работающего или спешки.
С точки зрения применения данного покрытия в кабеленесущих системах данный способ защиты подходит там, где исключена возможность «отслоения» краски от металла, что в дальнейшем исключает возникновения очагов ржавчины и может уменьшить нагрузочные характеристики системы и способствовать ее обрушению.
Хорошо подходит при прокладке электрических сетей малой мощности и слаботочных сетей в помещениях с дизайнерским оформлением, т.к. можно подобрать любой цвет по типам RAL.
Изделия покрытые порошковой краской соответствуют климатическим исполнениям УТ1,5, УТ2,5, УХЛ2,5, У3. Используются для типов атмосферы I по ГОСТ 15150-69 (категория коррозионности С1-С2).
2.3.4. Жидкие (алкидные) покрытия.
Алкидные краски для металла и древесины — это широкий ассортимент эмалей, отличающихся универсальностью применения, устойчивостью к истиранию, многообразием цветовых исполнений. В зависимости от модификации ЛКМ, покрытие может быть: глянцевым, матовым, полуматовым. Эти свойства во многом объясняются составом эмали, который включает алкидный лак и ряд наполнителей и растворителей. Также в состав ЛКМ входит композиция пигментов, от которой зависит цветовое исполнение покрытия. В настоящее время производятся алкидные краски для дерева и металла со специальными свойствами. Для этого, состав эмалей дополняется такими компонентами, как антисептики и антипирены. В качестве основных наполнителей может быть применен
мелкомолотый песок, мраморная или гранитная пыль и аналогичные материалы, выполняющие функцию загустителей. Главным компонентом в составе этих ЛКМ является алкидный лак. Этот компонент в свою очередь бывает двух видов: пентафталевый лак и глифталевый лак. Алкидные краски для наружных работ по большему счету производятся на основе пентафталевого лака. По сути, лак — это смолы, растворенные и тщательно перемешанные с растительными маслами, канифолью и глицерином. В то же время, именно составы, произведённые на основе глифталевого лака, практически не имеют пресловутого химического запаха, так как не содержат ароматических углеводородов. Поэтому, такие эмали рекомендованы для внутренней отделки помещений.
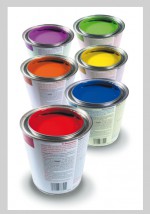
Алкидные краски для стен и других поверхностей характеризуются следующими преимуществами:
• наносятся большинством доступных инструментов, включая кисти, валики и пульверизаторы;
• быстро сохнут;
• сохраняют эластичность после полного высыхания;
• не утрачивают первоначальный вид после долговременной эксплуатации;
• устойчивы к долговременному воздействию ультрафиолетов;
• устойчивы к температурным колебаниям в диапазоне -60°С – +60°С;
• универсальны, так как могут наноситься на большую часть твёрдых поверхностей;
• представляют собой эффективную защиту от коррозии.
Среди недостатков следует отметить:
• небольшую толщину однослойного покрытия;
• наличие органических растворителей;
• возможность проведения покраски при температуре окружающей среды не меньше +5°С.
Инструкция применения алкидных эмалей практически не имеет эксплуатационных ограничений. Среди ассортимента данных лакокрасочных материалов можно подобрать средства, как для внутренней, так и для внешней отделки. Кроме того, эти эмали с одинаковым успехом могут быть нанесены своими руками на металлические, деревянные, пластиковые, бетонные и прочие поверхности. Нужно учитывать, что, независимо от того, что применяется, будь то обычные алкидные эмали или уретано алкидная краска для пола, высококачественный результат малярных работ возможен только лишь при соблюдении технологических предписаний. Технология нанесения этих лакокрасочных материалов предусматривает проведение подготовки поверхности (обезжиривание, очистка, шпаклёвка, шлифовка и нанесение грунта). Кроме того, необходимо в точности соблюсти рекомендации, приведенные в инструкции производителя, включая условия проведения малярных работ, количество слоев покрытия, количество примененного разбавителя и т.д.
В соответствии с классификацией, алкидные эмали характеризуются различными свойствами и, как следствие, разными способами применения. Узнать, к какому типу относится приобретенное средство, можно изучив параметры, указанные на заводской упаковке. Параметры приведены в буквенно-цифирном коде. Например, повсеместно распространённая алкидная эмаль ПФ-115 расшифровывается следующим образом: буквы ПФ означают пентафталевая, первая цифра 1 говорит о том, что лакокрасочный материал одинаково пригоден как для внутренних, так и для наружных работ. Последующие цифры являются каталожным номером. Кроме основных обозначений на упаковке можно встретить и другие цифры:
«0» — это обозначение алкидной эмали, которой можно не только красить, но и грунтовать поверхности;
«2» — покрытия, предназначенные для применения как в отапливаемых, так и в неотапливаемых помещениях;
«3» — покрытия, предназначенные для консервации и временной пломбировки оборудования.
«4» — гидрофобные эмали;
«5» — лакокрасочные покрытия со специальными характеристиками, например фосфоресцирующие или отпугивающие грызунов;
«6» – покрытия, устойчивые к воздействию бензина, масел и прочих ГСМ;
«7» – краска, устойчивая к различным химическим воздействиям;
«8» — термостойкие покрытия;
«9» – электроизоляционные или наоборот электропроводные эмали.
С точки зрения применения данного вида покрытия для кабеленесущих систем оно схоже с грунтованием и является его логичным продолжение. Оно дает возможность использовать предложенную заводом производителем гамму цветов и улучшить основные эксплуатационные характеристики и возможно внести новые, такие как термостойкость, стойкость к маслам и бензинам и другое. Ограничение в использовании алкидных покрытий является его слабая стойкость к механическим повреждениям и ограничение по температуре, скорости и качеству нанесения.
Изделия покрытые лакокраской соответствуют климатическим исполнениям УТ1,5, УТ2,5, УХЛ2,5, У3. Используются для типов атмосферы I по ГОСТ 15150-69 (категория коррозионности С1-С2).
2.3.5. Горячее, конвейерное оцинкование по методу «Сендзимира»
Среди известных способов горячего цинкования листов и полос, различающихся главным образом методами подготовки стали к цинкованию, основными являются «Сендзимир» или «Армко-Сендзимир», «Юнайтед стейтс стил», «Кук-Нортман» и «Селас». Для производства кабеленесущих систем самым популярным является металл оцинкованные по методу «Армко-Сендзимир».
В качестве исходного материала для цинкования применяется холоднокатаная неотожженная стальная полоса. На ее поверхности имеются остатки прокатной смазки, а также естественная оксидная пленка. Для подготовки поверхности полосы к цинкованию ее подвергают нагреву в печи с окислительной атмосферой до 350—500 °С. При этом загрязнения органического происхождения сгорают, а на поверхности стали образуется слой оксида железа толщиной до 3 мкм. Для активации поверхности стали полосу нагревают в печи с восстановительной азотно-водородной атмосферой при высоком содержании сухого водорода (75 %). Обычно термическую обработку полосы проводят при 750—950 °С с охлаждением до 450 °С перед погружением в ванну с расплавом цинка. Специальные газовые ножи сдувают излишки цинковой массы с листа при выходе листа из ванны. Это позволяет обеспечить равномерность слоя образовавшегося покрытия.
Толщина слоя оцинкования полосы зависит от скорости ее движения через ванну с цинком и может быть от 5 до 30 мкм. Для большинства иностранных производителей кабеленесущих систем принят стандарт использования полосы глубиной цинкового слоя 17-19 мкм. Это обусловлено тем, что при штрипсовании (автоматической резкой оцинкованной полосы нестандартной ширины) происходит «наплавление» мест среза в соотношении 1:4 к толщине цинкового слоя, т.е. слой на месте среза будет в 4 раза меньше слоя самой полосы. Если заметите, на большинстве оцинкованных изделий из полосы появление ржавчины начинается именно на местах среза.
Данный способ защиты востребован в кабеленесущих системах, т.к. позволяет ускорить процесс производства (исключить этапы очистки и флюсования на собственном производстве) и добиться равномерности покрытия при сохранении механической прочности, тем самым снизить стоимость изделия. Ограничением в применении является малая глубина слоя цинка (табл. 5), уменьшением на 30 % нагрузочных характеристик в сравнении с изделиями оцинкованными методом погружения.
Изделия из оцинкованной стали соответствуют климатическим исполнениям У2, ХЛ2, УХЛ2, УТ2,5. Используются в для типов атмосферы I по ГОСТ 15150-69 (категория коррозионности С1-С2)
2.3.6. Горячее оцинкование методом погружения
1742 год. Именно тогда французский химик и физик Поль Малуэн описал в докладе для французской Королевской академии метод оцинкования железа погружением в емкость с расплавленным цинком. За прошедшие столетия этот метод почти не изменился, и в его основе лежит все тот же процесс и те же химические реакции. Защита металла от коррозии достигается покрытием изделия из железа или стали слоем расплавленного цинка. Для этого изделие погружают в ванну с расплавом, температура которого примерно 460 °C. Под действием атмосферного давления происходит реакция чистого цинка и кислорода (Zn + O2) — в результате чего образуется
оксид цинка (ZnO), который вступает в реакцию с двуокисью углерода (ZnO + CO2). В результате, формируется карбонат цинка (ZnCO3). Это достаточно твёрдое соединение, которое обычно имеет серый матовый цвет. Именно оно останавливает дальнейшую коррозию металла. В 1836 году технология горячего оцинкования была усовершенствована французским химиком С. Сорелем, предложившим предварительно очищать металл 9%-ным раствором серной кислоты (H2SO4) и хлоридом аммония (флюсом). Технология горячего оцинкования базируется на принципе диффузии. Атомы цинка проникают во внешний слой стали во время погружения в цинковый расплав, и на поверхности образуется железо-цинковый сплав.
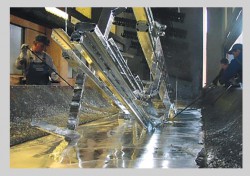
Современная технология горячего оцинкования металла практически совершенна и, помимо собственно оцинкования, включает 5 этапов подготовки поверхности и сам процесс:
1. Обезжиривание. При температуре 35 градусов по Цельсию с поверхности обрабатываемой металлоконструкции удаляют масла и другие синтетические загрязнения, затем следует промывка.
2. Травление. При температуре 20-25 градусов по Цельсию металлоконструкцию окунают в раствор соляной кислоты для удаления окалины и ржавчины с ее поверхности.
3. Промывка. Тщательно смывают остатки соляной кислоты.
4. Флюсование. При температуре 40 -50 градусов по Цельсию, изделие окунают в водный раствор хлоридов цинка и аммония. В процессе флюсования окончательно очищается поверхность, а также формируется пассивная пленка, которая блокирует последующее окисление и позволяет хорошо смочить деталь расплавленным цинком.
5. Сушка. Металл нагревают до температуры 100 градусов по Цельсию, тем самым удаляя влагу с его поверхности.
6. Горячее оцинкование металла.
Изделие погружают на 3-10 минут в емкость с расплавом, температура которого достигает 460 градусов по Цельсию. При извлечении конструкции из ванны на внешней поверхности дополнительно образуется слой чистого цинка. Таким образом, горячее оцинкование приводит к образованию двухслойного покрытия которое включает в себя железо-цинковый сплав и чистый цинк. Покрытие имеет среднюю толщину 70 — 150 микрон, что обеспечивает антикоррозийную защиту металлоконструкций на открытом воздухе в среднем 30 лет.
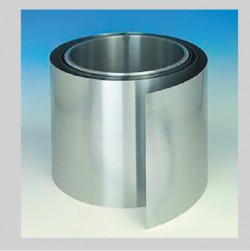
На качество цинкового покрытия влияют многие факторы:
- Температура расплавленного цинка и применяемая в нужных пропорциях химия. Технология горячего оцинкования требует поддержания температуры расплава на уровне 450-460 градусов по Цельсию. Это оптимальные условия для реакции между цинком и материалом обрабатываемой конструкции.
- Химический состав стали. В составе стали конструкций углерода и кремния должно быть меньше 0,25 %. Если горячему оцинкованию подвергается металл с содержанием кремния больше 0,25 %, ухудшается внешний вид поверхности.
- Очистка и подготовка поверхности перед цинкованием. При плохой очистке цинковый расплав ложится неравномерно и не вступает в реакцию со материалом изделия. В результате, покрытие получится с множествомсков, от этого на поверхности останутся непокрытые участки, или участки с плохим сцеплением и неравномерным покрытием.
- Скорость погружения в расплав. При погружении изделия в горячий цинк флюс постепенно плавится и гарантирует хорошую смачиваемость расплавом. Если скорость погружения слишком мала, то флюс расплавится раньше времени и поверхность покроется оксидной пленкой. Если же она слишком большая, – он не успеет полностью расплавиться, и покрытие будет иметь дефекты.
- Скорость поднятия из ванны. От скорости, с которой изделие вытаскивают из расплава, зависит толщина покрытия. Чем медленнее подъем, тем толще оно получится. Связано это со скоростью кристаллизации цинкового расплава. Для деталей разных размеров и форм оптимальную скорость подъема и наклон определяют индивидуально.
- Время выдержки в цинковом расплаве. Реакции цинкования проходят ровно столько времени, сколько температура изделия из стали остается на одном уровне с температурой цинкового расплава, поэтому время выдержки рассчитывают в зависимости от состава сплава, его толщины и типа конструкции.
В кабеленесущих системах, устанавливаемых на открытом воздухе, данный тип защиты используется повсеместно, т.к. толщина слоя цинка может регулироваться, в среднем от 45-70 мкм и достигать параметров 200 мкм, что значительно продлевает срок службы изделия. Механическая стойкость и прочность позволяет создавать конструкции по параметрам превосходящие другие типы защит.
Изделия покрытые цинком путем погружения, соответствуют климатическим исполнениям У1, ХЛ1, УХЛ1, УХЛ5, УТ1,5. Используются для типов атмосферы II по ГОСТ 15150-69 (категория коррозионности С3-С4)
2.3.7. Нержавеющая сталь.
К нержавеющим сталям относят группу коррозионностойких сплавов на основе чугуна с содержанием минимум 10,5 % хрома и низким содержанием углерода. В результате контакта с кислородом из окружающей среды (воздух, вода или другие среды) на поверхности нержавейки образуется тонкий, в несколько слоев атомов, прозрачный слой окиси хрома. Слой защищает изделия из нержавеющего сплава от дальнейшего химического влияния. Если поверхность повреждена, пассивный слой создается автономно под влиянием кислорода.
Основные преимущества изделий из нержавеющей стали:
• Высокая прочность
• Стойкость к температурным воздействиям
• Высокая коррозионная стойкость
• Отсутствие выделения вредных веществ при пожаре или механической обработке.
Применение конструкций из нержавеющей стали целесообразно при использовании оборудования в пищевой и медицинской промышленности, в особо агрессивных окислительных средах и на химических предприятиях, где необходима высокая коррозионная стойкость. Также используется один из видов нержавеющей стали для особого применения – несущие конструкции в транспортных тоннелях где очень высокое содержание серы.
Изделия из нержавеющей стали соответствует климатическому исполнению У1, ХЛ1, УХЛ1, УХЛ5, УТ1.5. Используются для типов атмосферы III и IV по ГОСТ 15150-69 (категория коррозионности С5 и С5-М).
3. Техническая информация.
При создании кабельных трасс необходимо учитывать множество параметров для правильного их заполнения кабелями и их установки. Основными являются:
1. Общие климатические условия строительства:
a. Снеговой район.
Снеговая нагрузка влияет на общую нагрузку, которую должны выдержать верхние лотки (крыша), полки и стойки эсткады. В нашей стране 8 снеговых районов и снеговая нагрузка колеблется от 80 до 560 кгс/м2 этот выбор обязательный. Выбор снеговых районов (см. Приложения, Рис. 1).
b. Ветровой район.
Ветровая нагрузка влияет на общую парусность всей системы и учитывает боковые составляющие силы, высоту здания и другие факторы, описанные в актуальной редакции СНиП 2.01.07-85. (см. Приложения, Рис. 2).
c. Район/место установки.
Влияет на общее расчетный эксплуатационный срок кабельной системы исходя из параметров ухода цинка. Расчет ведется на основании замеров/данных службы коррозионной защиты или опираясь на способ установки системы по таблице 5 стандарта ISO 12944. «Атмосферно - коррозионные категории и примеры типичной окружающей среды»
d. Виды грунтов.
Определяет строительные параметры фундаментов и глубину их установки.
2. Параметры электрической сети.
a. Тип кабелей.
i. Силовые кабели
- Класс напряжения.
a. До 1 кВ. Прокладка отдельно или совместно с контрольными кабелями с перегородкой или над силовыми кабелями свыше 6 кВ.
b. Свыше 1 кВ. Необходимо учесть количество соединительных муфт, установку коробок транспозиции, расчет креплений по динамическим нагрузкам от токов короткого замыкания. Прокладка кабелей осуществляется в плоскости или треугольником (в случае применения одножильных кабелей).
- Тип изоляции.
a. Изоляция из сшитого полиэтилена/этиленпропиленовой резины. Исходя из требований ГОСТ-Р 55025-2012, необходимо учесть радиус поворота кабеля равный 15*D (диаметр кабеля), т.к. кабель с диаметром более 35 мм не удастся уложить в стандартный поворот
радиусом 500 м. Необходимо применять повороты радиусом от 500 до 1000 мм.
ii. Контрольные и сигнальные кабели.
Данные кабели всегда прокладываются отдельно от силовых кабелей свыше 1 кВ и требует соблюдение разделов ПУЭ 2.3.120, 2.3.124.
iii. Специальные кабели. Например: неэкранированные кабели для питания двигателя от частотного преобразователя и не имеющего выходного фильтра имеют неоднородность выходных синусоидальных гармоник при высоких пиковых скачках напряжения (до 4 кВ). Данные помехи обусловлены использованием IGBT-транзисторов и ШИМ-модуляции. Для прокладки по эстакадам данные кабели экранируют в случае их прохождения в одном лотке с 1 кВ кабелями или контрольными через разделитель. В случае использования неэкранированного варианта кабелей следует их прокладывать в отдельном лотке от контрольных или с разделителем в случае 1 кВ
кабелей.
b. Вес кабелей и их количество.
Вес кабелей в зависимости от вида их прокладки будет влиять на нагрузку на лоток и на полку, в зависимости от расстояния между местами крепления лотка к полкам.
ВАЖНО: Параметры веса кабелей указываются производителями в своих каталогах продукции. Из-за разной конструкции и применяемых материалов параметры у одинаковых типов кабелей могут отличаться!
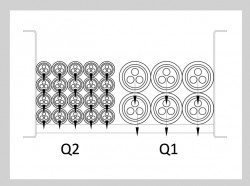
Формула для расчета кабельной нагрузки на погонный метр:
Qk=(N1*q1+N2*q2+…+Nn*qn);
Где: Qk – погонная нагрузка от кабеля (Н/м).
N1 – количество кабелей первой группы (шт)
q1 – удельный вес кабеля первой группы (Н/м)
Qsys= Qk+Qc+Qz
Где: Qsys – погонная нагрузка на кабельный лоток (Н/м).
Qk – погонная нагрузка от кабеля на метр (Н/м)
Qc – погонная нагрузка от снега на метр (Н/м)
Qz – погонная нагрузка запаса на метр (Н/м) (по ПУЭ не менее 15 %).
Данный параметр согласно ГОСТ Р 52868-2007 называется безопасная рабочая нагрузка (БРН), которая зависит от расстояния. У иностранных производителей это нагрузочная характеристика изменения кабельного веса и расстояния между пролетами. Данная характеристика обязывает производителей кабельных конструкций испытывать все свои изделия на прочность с коэффициентом запаса 1,7 при прогибе не более 10 % от расстояния. Например, характеристики конструкций соответствующие ГОСТ Р 52868-2007: кабельная нагрузка 100 кг/м при пролете 6 метров. Это значит что конструкция испытана при весе 170 кг/м и имеет прогиб 59 мм (не более 10 %) на расстоянии между точками крепления 6 метров. В случае увеличения нагрузки, прогиб может увеличиться и возможно приведет к повреждению либо обрушению конструкции.
ВАЖНО: Производители, которые гарантируют качество своей системы, дополнительно с нагрузочной кривой указывают параметры прогиба в мм.
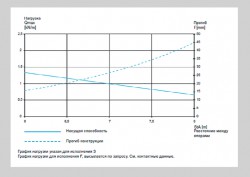
В случае, выбора консоли для установки лотка необходимо использовать следующую формулу:
P= (Qsys + W) * L
Где: P – нагрузка на консоль (Н).
Qsys – погонная нагрузка на кабельный лоток (Н/м)
W – вес кабельного лотка и необходимых аксессуаров (Н/м)
Lопор – расстояние между опорными точками (м)
ВАЖНО: 1 кг= 9,807Н
c. Наружный диаметр кабелей и их количество.
Данный параметр влияет на заполняемость лотка или на длину полки, к которой кабель будет зафиксирован исходя из способа прокладки (в плоскости или треугольнике). Необходимо знать наружный диаметр кабеля, класс напряжения, как следствие регламентируемое расстояние между кабелями или объем пучка. Формула для расчета полезного сечения кабеля:
S=D*D/100
Где: S - площадь полезного сечения (см2).
D - диаметр кабеля (мм)
ВАЖНО: Параметры диаметров кабелей указываются производителями в своих каталогах продукции. Из-за разной конструкции и применяемых материалов параметры у одинаковых типов кабелей могут отличаться!
Необходимое условие для подбора полезного сечения лотка:
N1*S1+N2*S2+…+Nn*Sn ≤ F
F=A*B
Где: F – полезное сечение лотка (см2).
N1 – количество кабелей первой группы (шт)
S1 – количество кабелей первой группы (см2)
А и В – геометрические размеры полезного сечения
лотка, (см)
d. Разветвленность точек подключения.
Данный параметр влияет на количество уровней эстакады.
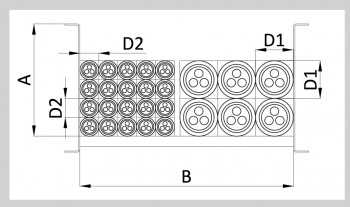
3. Маршрут трассы.
Влияют на сложность строительных работ, типы и места установки фундаментов, количества поворотов и подъемов трассы, места подключения и перехода в точки подключения.